How Leather is Made
How is upholstery leather made? Here we break down the process.
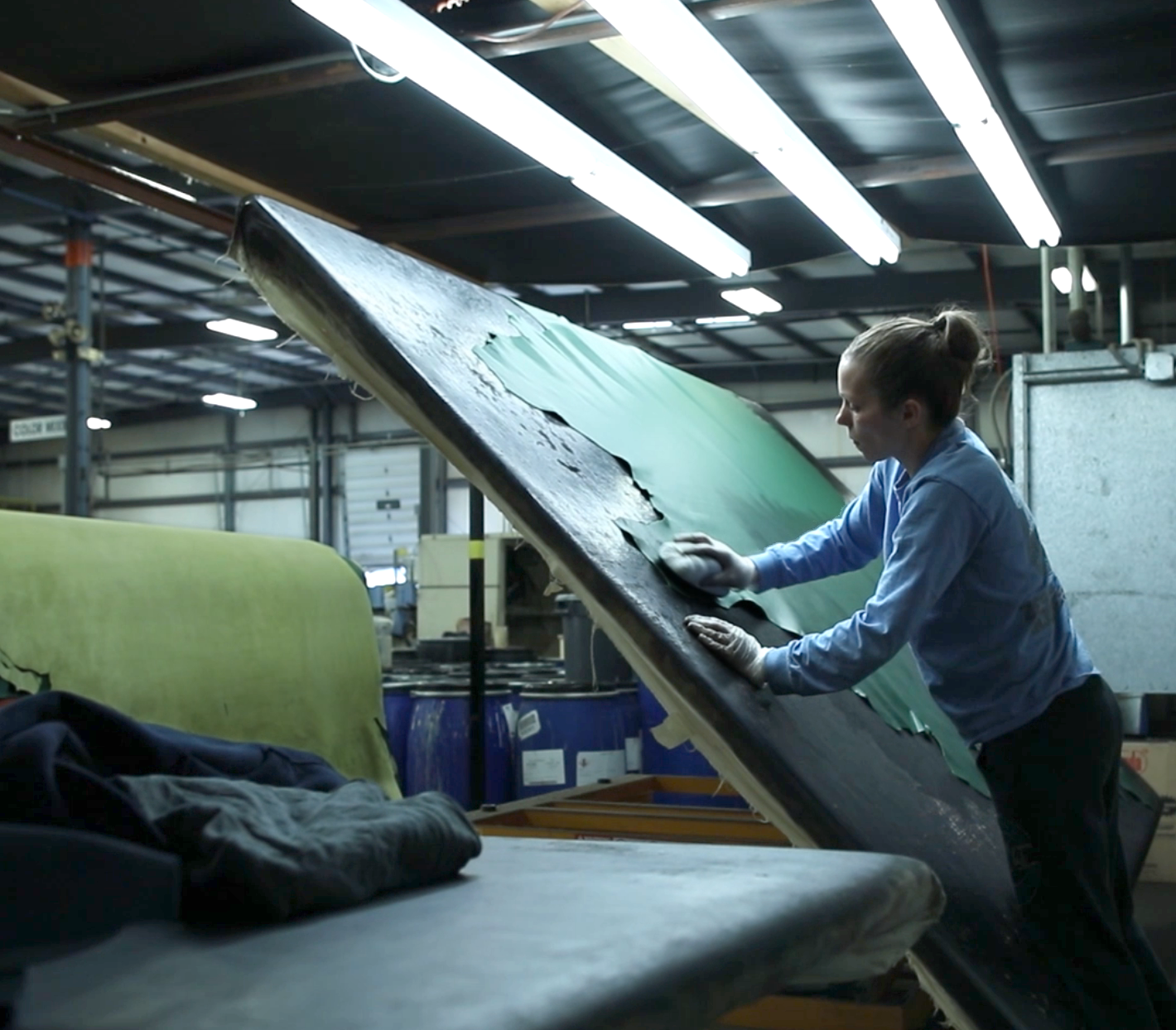
The first important fact to understand about making upholstery leather from bovine/cattle is that 100% of leather hides are a by-product of the meat and dairy industries. No animal is raised for their hide for leathermaking at Cortina. If not for the leather industry, all hides would be disposed of in a landfill and go to waste, and studies show that is more devastating to the health of our environment than modern leathermaking.
Leathermaking is a thousand-year-old art form that has changed drastically in the last 40 years due to pressure to consider environmental and labor concerns. Cortina Leathers has a strict policy to only source hides from responsible, commercial tanneries that also have strict commitments to social and environmental stewardship such as the U.S., Italy, and Germany to name a few. We do not source hides from India, China, or Pakistan, countries that have made improvements recently, but still don't meet Cortina's standards of social responsibility.
Making leather has many steps which can't be automated because each hide is unique and excess waste in manufacturing is cost-prohibitive. Luxurious and durable hides that meet Cortina's high product standards require human interaction with every single hide all the way along the process! There are four main steps to making upholstery leather:
1. Preparation
2. Tanning
3. Retanning
4. Finishing
1. Preparation
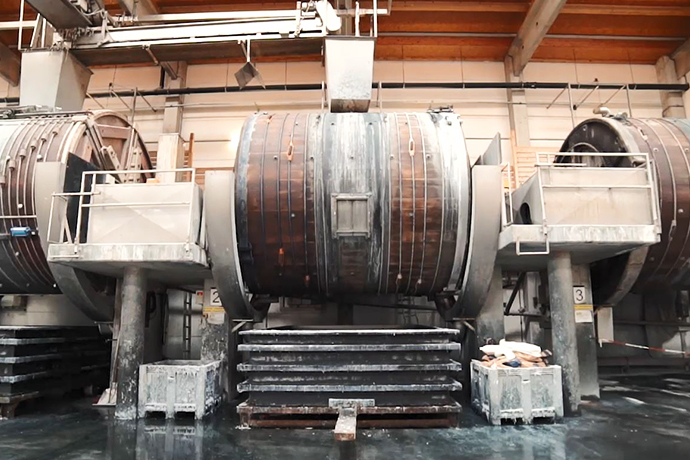
Environmental StatementThe preparation process prepares the hide for tanning and consists of curing, soaking, liming, fleshing, splitting, deliming, bating and pickling. The first step, curing, takes place prior to the tannery to ensure the hides do not spoil before arrival at the tannery. The highest quality pure aniline leathers are made from fresh hides which are not cured--requiring quick transport from the raw hide supplier to the tannery.
The remaining steps of preparation occur in large wooden or steel drums in the section of the tannery known as the beamhouse. In the beamhouse, the hides are cleaned and unwanted materials such as hair and flesh are removed so that only the fibrous collagen structure that gives leather its strength and flexibility remain. The collagen structure is also expanded and softened so that it better accepts the tanning chemicals. These steps determine the softness and stretchiness (elongation) of the leather, so are typically tightly controlled by the finisher or tannery.
Also during preparation the hide is split to separate it into the top-grain layer and the flesh split. The top-grain layer contains the fibrous collagen section and so is used for most high-quality upholstery leathers requiring strength, durability and softness. The flesh split is typically used to make suede leather, lower-durability split leather or dog bones.
Beginning in 2024, the majority of hides Cortina uses to manufacture finished leather at our U.S. facility will have their unusable edges pre-trimmed prior to tanning. Pre-trimming is costly, but it has important benefits for our environment. Learn more in the Pretrimming section on Cortina's Environmentals Stewardship page.
2. Tanning
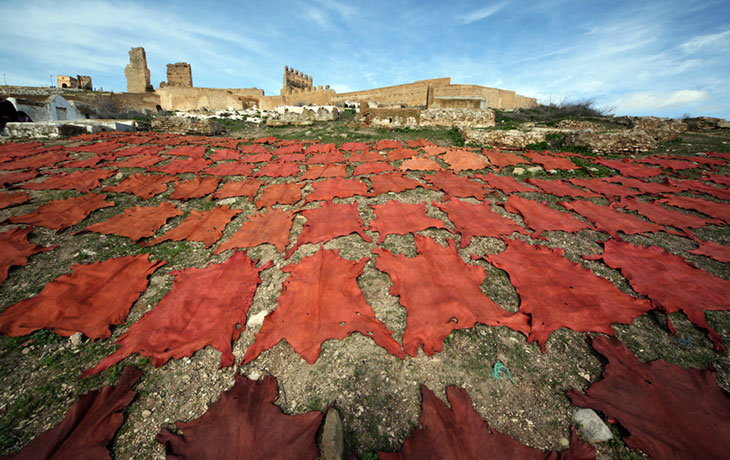
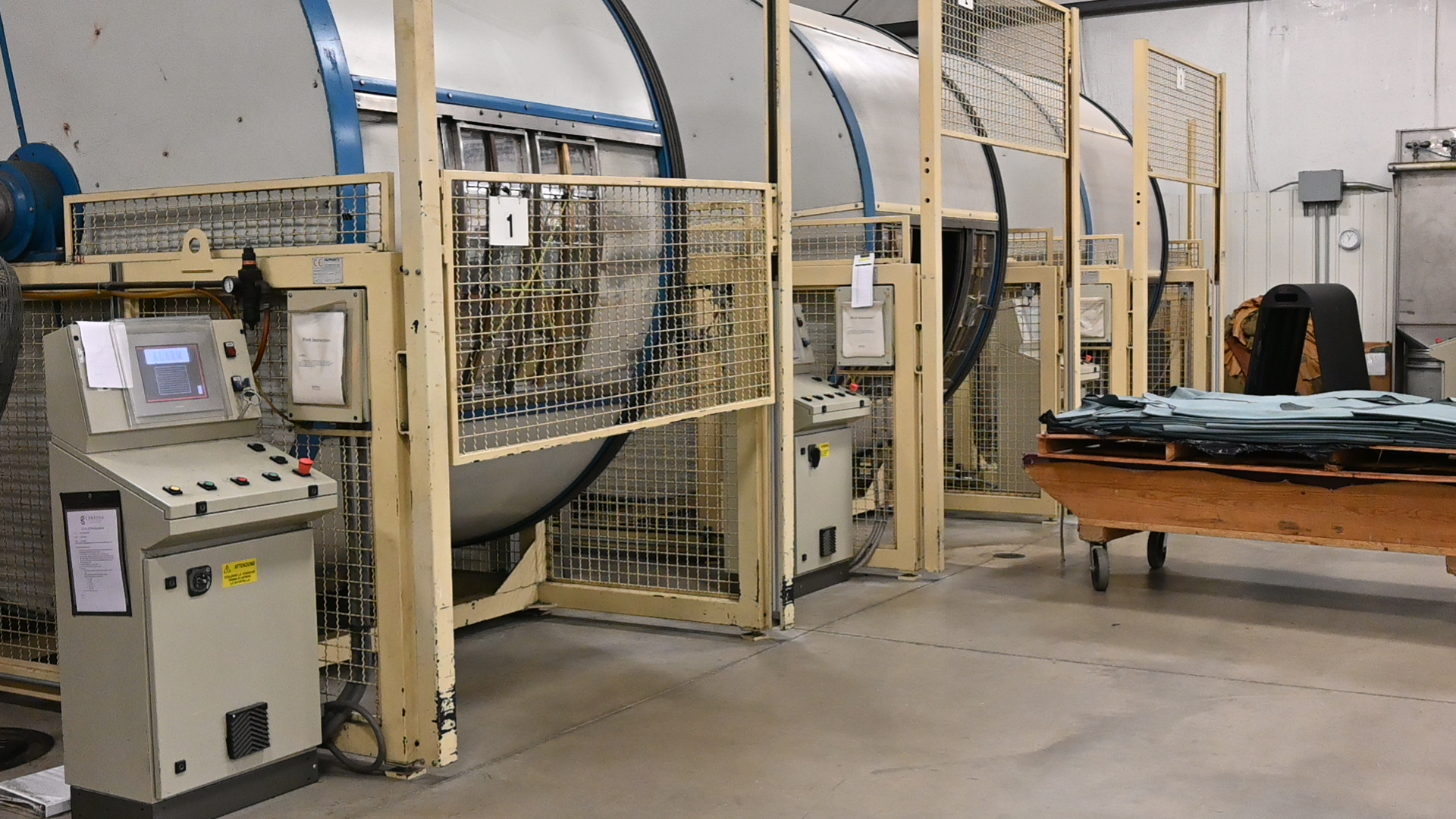
The Tanning process converts the perishable hide to leather which is non-perishable, strong, flexible and stable under varying conditions of heat and moisture. Tanning steps include tanning, samming and shaving. Tanning occurs in large drums which slowly rotate so that the tanning agents (commonly known as “liquors”) are slowly worked into the full thickness of the hide. There are three common types of tanning, all of which are used for different leather lines by Cortina Leathers:
Chrome tannage
Approximately 90% of all upholstery leather including the majority of Cortina Leathers is chrome tanned due to its superior softness, acceptance of bright colors and resistance to water and to shrinkage at high temperatures. Note: Only trivalent chromium 3 is used in the tanning process—not the hexavalent chromium 6 variety which is considered harmful to humans and the environment. The use of Chromium 3 in tanning was a concern prior to advances in chemistry that prevent the trivalent chromium from oxidizing into hexavalent chrome, and advances in waste-water treatment that prevented the release of chromium into the waste stream, but this is not a concern in modern tanning operations with which Cortina sources crust and hides.
Chrome-free tannage
Tannage type where chemicals such as glutaraldehyde, oxazolidine, formaldehyde, aluminum, zirconium or synthetics are used instead of chromium in the tanning process. Chrome-free tanned leather is typically a bit firmer and stiffer than chrome-tanned, has lower tear strength and exhibits shrinkage between 70-85ºC. The vast majority of chrome-free leather is used on European automobile seating.
Vegetable tannage
The original tanning process where tannins from tree bark combined with vegetable extracts such as mimosa are used to preserve the leather. Vegetable tanning through the use of vats, which can take up to a year, creates a strong, dense, firm leather typically used in shoe soles, equestrian leather such as saddle, harness and bridle, or in furniture applications such as for strap chairs, director’s chairs or pull handles. However, drum-tanning with vegetable extracts can produce a softer leather that can be used in upholstery.
After the tanning step, surplus water is removed by samming and then the leather is shaved to the desired final thickness. Most upholstery leathers are shaved to between 0.9-1.3mm. However, heavyweight upholstery leathers can range as high as 1.6mm before sewing and upholstering becomes challenging.
At this point, the leather is known as either “Wet Blue” if it is chrome-tanned, or “Wet White” if it is Chrome-free or vegetable-tanned.
3. Retanning
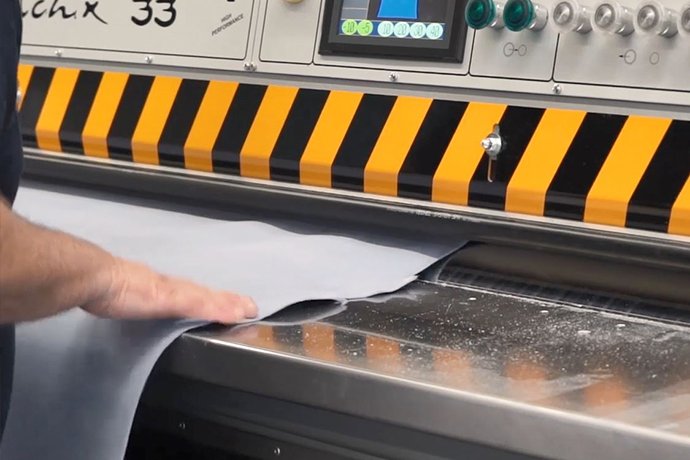
In the retanning process, the leather is given its required specific properties for each leather line or product, as defined by the finishing house or customer. Softness, fullness, density, elongation, the break of the leather, the leather color, etc. are all adjusted or imparted in the retanning process. Steps in the retanning process include neutralization, aniline dying, retanning, softening, drying and buffing the leather.
All the steps prior to drying occur in wood or steel drums ranging in size from 10 to 300 hides. Most high quality leathers, including all Cortina Leathers, are aniline dyed in the drum. In this process, a rich color is achieved by introducing aniline dyes to the drum mix which is slowly turned until the color penetrate throughout the thickness of the hide. A range of drying methods including vacuum drying, toggling, or suspension drying.
Some examples of how different leather characteristics are created in the retanning process: For a firmer leather, vegetable-extract can be added in the retanning step. For a softer, more stretchy leather, additional fatliquors and a longer soaking period can be utilized in the softness step, or a similar result can be achieved by drying without stretching. By adjusting the many variables in different combinations, an almost infinite number of unique leathers can be created.
Each of the 50+ leather lines offered by Cortina Leathers has a unique retanning process and formula. At the conclusion of the retanning process, the leather is known as crust. At this point it is typically transported to a leather finisher.
4. Finishing
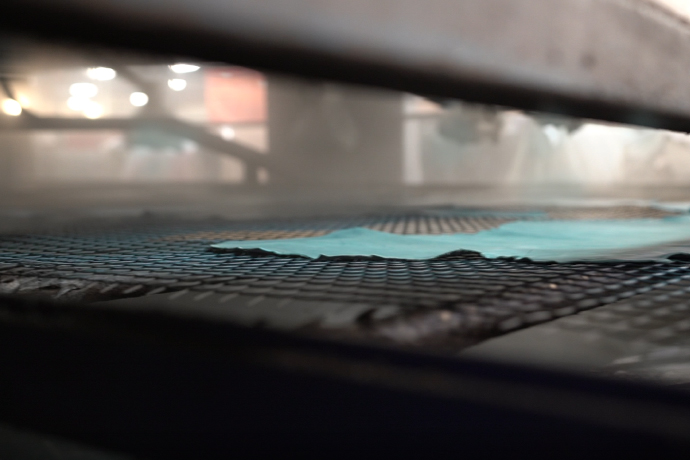
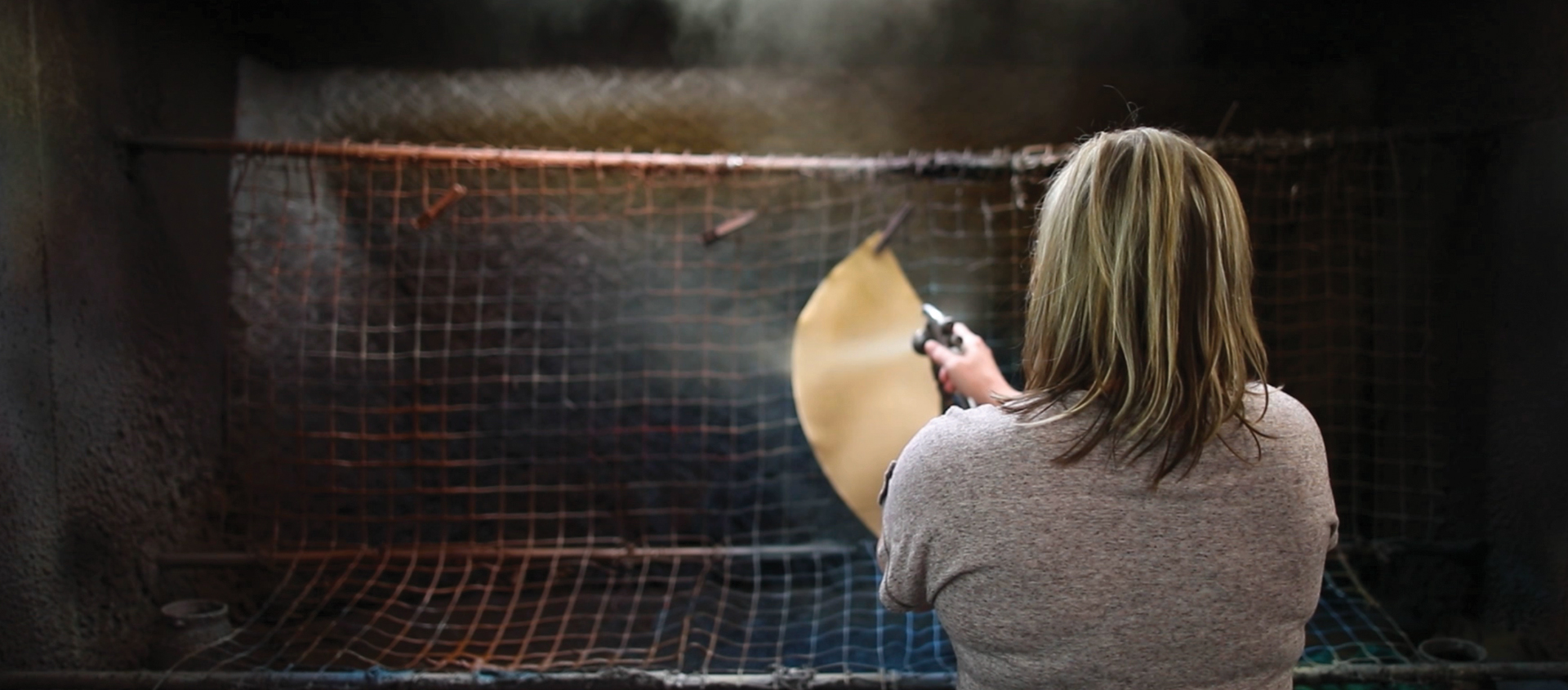
The process of leather finishing creates the final desired characteristics of the leather such as look, color, sheen, protection level, grain, and hand. Because Cortina is a finishing facility, making custom leather is easy! Twenty percent of Cortina’s output is custom-made to meet clients’ precise requirements.
Steps to finishing leather include milling, staking, oiling, waxing, rolling, spraying, topcoat application, embossing, hand-rubbing, finiflex, ironing, and more. However, not all steps are applied to each leather. For example, a pure aniline leather may only get a wax treatment followed by a cold-rolling for sheen, while an automotive leather may be embossed with a manufacturer-designed pattern and receive a stucco application, two color coats and a clear topcoat, all with strong cross-linkers and binders to create a the strong protection required to withstand the rigors of heavy use and spills.
By varying the finishing steps, settings at each step and the formulations of each treatment, leather finishers can create all leather types (pure aniline, aniline, semi-aniline or pigmented) in with crust prepared with the same preparation, tanning and retanning process. Within a category many different looks can be created. For example, aniline leathers can be finished to look distressed, have a high-burst pull-up, be smooth and glossy or with a large, natural pebble and a matte, draggy hand.
Leather finishers typically focus in certain areas of expertise. It is for this reason that Cortina Leathers utilizes its own finishing operation in Ohio along with several in Italy to create the wide variety of finishes desired for its markets.